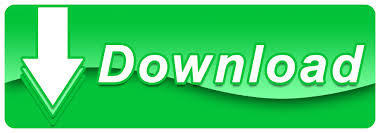
Common causes of discolored solder mask include using different flux components, mixing several batches of PCBs during wave soldering, and changing the type of solder mask or its thickness halfway through the process.ĭiscoloration of the solder mask is also a familiar wave soldering defect that plenty of printed circuit board manufacturers encounter. Finding discolored costumes can be easily identified on your PCB, on the solder resist, the conveyor belt, or even in the wave soldering equipment. Discoloration of Solder MaskĮven though the stain of the solder mask may come as a cosmetic issue, its causes need to be investigated thoroughly by your manufacturer. But again, reduced application of welding resist is a common defect that plenty of PCB designers face. Only the areas that require the welding should be left exposed for wave soldering to avoid defects on the board. However, when it comes to wave soldering of PCBs, the application of solder resist is a big challenge that faces plenty of PCB board soldering technicians. It also prevents the board from mechanical problems during the process of wave soldering. For instance, solder resist protects a PCB from mechanical challenges and corrosion. Solder mask or solder resist on the printed circuit board does perform several essential functions worth noting. Solder resist is an integral part of PCB technology. As soon as you get rid of the soldering iron immediately to avoid cases of dry bones, hence gaps in the solder joints Before allowing changes, make sure that the solder on the joint coolsĥ. Ensure that the components to be soldered are tightly secured to avoid movement during the soldering process as this may bring about gaps in the solder jointĤ.
#Pcb soldering free
Ensure that the entire surfaces that need soldering are free from greaser and cleanģ. All is not lost, though, as there are a few pointers that can help designers develop solder joints. Unfortunately, differences in the solder joint are typical wave soldering defects that plenty of printed circuit boards soldering technicians face.ġ. Weak solder joints with gaps in them will either make the equipment not function as desired or a possibility of the solder joint falling intermittently. When it comes to soldering PCBs, ensuring that that the solder joints on the board are in the right way is of importance in electronics construction. If designers fail to control the welding content and the welding position, defects such as the following may occur.
#Pcb soldering manual
Since wave soldering is a process that involves machinery, it means that accuracy is slightly higher compared to manual welding. Unlike manual soldering, wave soldering is slightly faster, not forgetting the fact that it can produce high-quality products. Wave soldering is an active process that is suitable both for surface-mount assemblies also traditional through-hole assemblies. Wave soldering finds its name from the wave of solder that each board passes over. Waver soldering allows PCB manufacturers to efficiently and reliably solders huge printed circuit boards. Wave soldering is a unique soldering process mainly used when manufacturing printed circuit boards in bulk. So, what are the most common wave soldering defects that PCB soldering designers face? This article is a comprehensive list of 10 most typical wave soldering defects and its solutions. Unfortunately, though, there are common problems that PCB designers face during wave soldering. Its name comes from the process of connecting the metal components to a printed circuit board by the use of molten solder waves. Wave soldering is commonly used for soldering surface mount components and through-hole mounting devices through the hybrid assembly. For more than two decades and counting, wave soldering has been relied upon by PCB designers for PCB mounting, to the extent of becoming a fully grown electronic mounting solution.
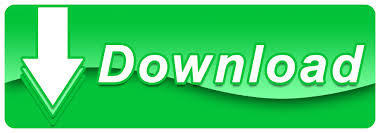